Introduction
Standardized rubber O-rings are crucial components in various industries, guaranteeing that equipment runs efficiently and without loss through leakage. Although these small, circular sealing elements might seem unimportant, their usage is crucial for the functionality and productivity of numerous machines, engines, and devices. O-rings function to ensure that two different surfaces fit together in a way that liquids and gasses cannot diffuse through and this is paramount for a number of systems.
Before analyzing the need of producing custom rubber O-rings, it is essential to look at their uses and the composition of the rubber. It is worth pointing out that these O-rings can be modified to suit certain needs, which things that ordinary, generic products cannot provide. Their customization guarantees high efficiency in various circumstances that makes their applicability impossible to imagine in many sectors.
What Are Custom Rubber O-Rings?
Custom rubber O-rings are small sealing devices that are manufactured from various types of rubbers to suit various uses in different applications. These are rings made up of a circular structure that is utilized to form a seal between two surfaces to avoid cases of leakage of either fluid or gases. The customization component enables one to vary the size, material type, and characteristics of the O-rings as per the specific demands of the equipment or system in which they will be placed.
Hereby, the use of the proposed approach for O-rings manufacturing has advantages over making standard O-rings. They can be designed to suit specific applications where temperatures are high or pressures are applied or where they have to deal with various chemicals. Thus, they ensure a good seal in the most critical conditions, increasing the performance and reliability of the equipment and apparatus, where they are used.
Importance of O-Rings in Sealing Solutions
O-rings are crucial in sealing systems to ensure that they do not leak, which may cause ineffectiveness, destruction, or total failure of the system. The O-rings find greater importance in industries like automobiles, airplanes, and healthcare products which require superior accuracy and durability. These small parts allow for proper containment of fluids and gasses in specific regions, which is important for many devices and machines to run effectively.
Some of the implications of various systems not having O-rings are that they would require additional sealant, product loss may occur and could cause damage to the environment, and would lead to further frequent service calls and costs. Rubber O-rings ensure the equipment possesses great durability since human beings will not have to repair the equipment frequently. Another factor that has been attributed to the valve’s enhanced capabilities for preventing leaks is its contribution to the safety and reliability of the systems that incorporate the same.
Types of Rubber Materials Used in O-Rings
Natural Rubber
Natural rubber provides high elastic properties and tensile strength, which makes the material suitable for use in applications where flexibility is desirable. It is often employed in cases where the O-ring is subjected to regular stresses and strains and still maintains its original form and size. This material is preferred because of its high resilience and because it becomes malleable when it is deformed.
While natural rubber has its advantages, it has some disadvantages in chemical and thermal performance. This material is not ideal for use in areas where it experiences contact with oils, fuels or where the surrounding environment is characterized by extremely high or low temperatures. Nevertheless, owing to the higher mechanical strength, it has been widely used in many common purposes.
Nitrile Rubber
One of the most common artificial rubbers is nitrile, or Buna-N, which is very resistant to oils, fuels or any other chemicals that it comes across, making it ideal for car production. Among the strengths one can single out its ability to create a very tight fit to the zones where it is in contact with petroleum-based fluids. This makes nitrile rubber O-Rings to be critical in the fuel systems, hydraulic systems and other machinery that is in contact with oil and fuel.
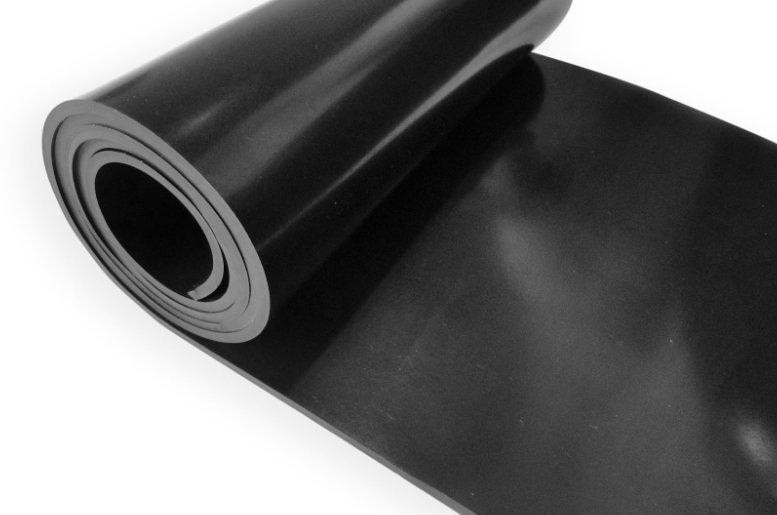
It also has good non- chemical resistance, mechanical properties such as abrasion and wear, and is also very durable. These qualities make it possible for the tolerance O-rings to perform well when made from nitrile rubber and penetrate hard conditions. Nonetheless, it should be noted that this material has lower mechanical characteristics when exposed to heat or when applied to highly flexible objects.
Silicone Rubber
Silicone rubber has outstanding temperature stability characteristics, both high and low those that enable its usage in various fields. It is capable of sealing at a temperature range of -60°C to + 200°C. This makes it possible for the silicone rubber O-rings to be suitable for applications that are characterized by big changes in temperatures.
Also, the silicone rubber is chemical and thermal resistant, biocompatible and non-toxic as a perfect material regarding the medical and food-grade markets. It also makes silicone rubber O-rings to be suitable to use under various temperatures to make sure that they offer their sealing services in vital sequence in instances like in medical uses and in the food industry.
EPDM Rubber
Furthermore, EPDM rubber possesses excellent properties of weathering, ozone, and UV resistance, which are particularly desirable for applications of automotive parts and other outdoor products. This material is stable and does not decay when exposed to the conditions and environment, making it suitable for use in products such as window and door gaskets and those cooling systems where the gasket must resist solutions such as antifreeze and the like.
Apart from that, EPDM rubber has good chemical resistance to most chemical solutions such as acids and alkalis, and of course, it has good resistance to boring and other erosive weather. This makes it a useful product that can be used in different industries and car manufacturing industries due to chemical susceptibility.
Viton Rubber
Viton rubber is a type of fluoroelastomer that is famous due to its outstanding particularity such as chemical resistance and high temperature qualities. It can be exposed to a wide range of chemicals such as fuel, oil, solvent and many acids without diminishing the sealing capabilities. This makes Viton rubber O-rings ideal for use in abrasive conditions such as in the oil and maximal industries or processing industries.
Besides offering chemical resistance, Viton rubber has fairly good high-temperature capability and can resist temperatures of as much as 250° C. This makes it very suitable for the manufacturing of Viton rubber O-rings, which have excellent high-temperature and chemical resistance, making them suitable for some of the severest environments.
Advantages of Custom Rubber O-Rings
Versatility
Standard rubber O-rings are quite versatile, but custom rubber O-rings are significantly more useful because they can be designed to meet the needs of any project, even if the specifications are unusual. This customization makes the O-rings offer maximum seal and increases the efficiency and reliability of the system where the O-rings will be used. In the automotive, aerospace, medical, food industry or any other industry, an O-ring can be Custom Made to fit a unique call for performance.
Customizing O-rings also provide a possibility to produce these elements from a broad range of materials, each being selected according to the desired properties of the element. It results in the selection of materials that provide the maximum durability, chemical stability, high temperature characteristics, and flexibility of the O-rings and their operating conditions.
Durability
The most beneficial aspect of rubber O-rings has to do with their service life. These O-rings have been developed to provide resistance to the environment and extreme conditions hence they have long service lives and replacement frequency is low. This durability does not just guarantee longevity in the performance of the products but also a long-term financial advantage as it cannot be compared to normal products that are usually subjected to frequent repairs, replacements, and breakdowns.
Custom rubber O-rings durability is as a result of proper materials choices and production methods that ensure the rubber O-rings will not wear or develop rapidly. As materials used for fabrication of custom O-rings allow their application in environments characterized by certain parameters, for example, temperature, chemicals, and mechanical stresses, their sealing capabilities are likely to be effective in delivering present application requirements.
Applications of Custom Rubber O-Rings
Automotive Industry
Custom rubber O-rings are also essential in the automotive industry to meet the components’ functionality requirements. It is applied in engines, brakes, and transaxles to prohibit dripping of fluids and preserve efficiency. For example, silicon or rubber O-rings used in fuel injectors and oil filters require a tight fitting seal to avoid fluid leakage that can compromise the operational efficiency of an engine.
Similar to the seal applications, custom rubber O-rings are applied in automotive air conditioning systems to ensure it remains secure and functional. The ability to cope with high pressures and temperatures in these systems necessitates these components in the maintenance of the reliability and performance of modern automobiles.
Aerospace Industry
Custom rubber O-rings play an essential role in sealing hydraulic systems, fuel systems and cabin pressure systems in the aerospace industry. In an environment with such high risk, it is critical that the seals, specifically O-rings, are highly dependable, and even the tiniest flaw may lead to major mishaps. Technical O-rings produced to standards of the aerospace industry enable safer and more efficient operation of aircraft.
Apart from their application in hydraulic and fuel systems, the customized rubber O-rings are also applied in the systems including, but not limited to, aerospace landing gear, aerospace engines, and aerospace environmental control systems. The specific qualities of these parts, including their durability and capability to work under high temperatures and pressures, make them crucial to the operation and safety of aircrafts.
Medical Industry
Custom rubber O-rings are also commonly applied in the medical industry being used in syringes, pumps, and diagnostic devices, among others. These O-rings incorporate the most vital closures necessary for finishing the correct operation of medical tools, favorable for patient security as well as medical procedures. For instance, an O-ring that is used in an infusion pump needs to form a strong seal so that it does not leak or cause undesired flow to occur to the pump’s control of substances such as medication.
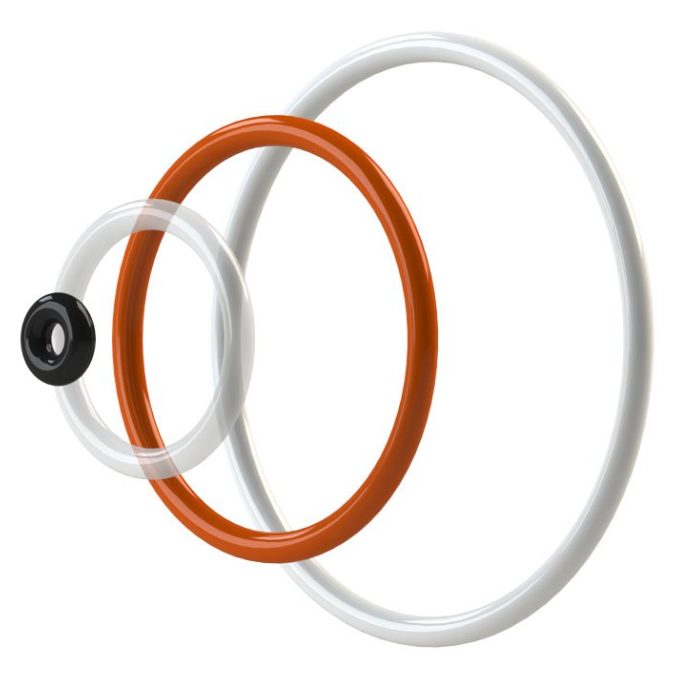
In the medical industry it is common to use custom made rubber O-rings of biocompatible materials like silicone which can be easily sterilized for use with delicate applications. Due to the fact that they offer reliable seals for use when developing different medical devices, they offer a way to guarantee that patients are not at risk.
Food and Beverage Industry
This is especially important in the food and beverage industry where custom rubber O-rings should indeed meet safety and hygiene requirements that must be met. Its common uses include in processing lines and packaging equipment for foodstuff to avoid cross contact and safeguard the purity of food. For instance, O-rings in bottling machines and mixers, or gate valve stems in pipelines, may be susceptible to very high stresses during moderate motions.
needs to have a durable and airtight closure that is designed to keep out contaminants while ensuring the quality of the food and beverages to be processed.
As for the specific product, food and beverage industry applied custom rubber O-rings tend to be developed from the materials that have been approved for use in food processing and are also resistant to cleaning chemicals. They offer the possibility of a high seal to be maintained at all time through frequent sessions of washing and sterilization making them very important in food safety and overall product quality.
Oil and Gas Industry
It is in this respect that we find that the peculiar specifications for the oil and gas domain are centered around developing an O-ring product that is capable of withstanding pressure and functioning well in severely corrosive environments. These rubber O-rings are made to provide custom fit for a particular function and are used in drilling equipment, pipes and valves to boost the efficiency and effectiveness of these units. It allows them to provide a secure closure to environments in such circumstances and, thereby, minimize the likelihood of escapes and pollution.
They also have various types of material and from what we have used in oil and gas are the custom O-rings in Viton material which is very effective since it has chemical and high temp –resistance. This also enhances the ability of O-rings to endure the environment in E&P operations until a good sealing is formed, which enhances safety and efficiency of all the processes in the oil and gas industry.
Electronics Industry
In the electronics industry, custom rubber O-rings are found in connector applications to provide protection to delicate items such as connectors from moisture, dust, among other elements. This is a critical factor in their ability to create a sealed environment that is conducive for the proper functioning of electronics devices. For instance, O-rings in waterproof cases and enclosures help to ensure that further integrated electronic elements in such gadgets are not affected by water or dampness.
The standard O-rings used in the electronics industry may be manufactured from various types of materials that can withstand different weather conditions and other outer forces so as to create a high quality seal in any particular use. Due to their ability to safeguard electronic components and shield them from physical impact and environmental contaminants, it becomes significant to consider them integral in the longevity of the electronic devices.
Factors to Consider When Choosing Rubber O-Rings
Temperature Range
Another important aspect in selecting rubber O-rings is the service temperature range. The O-ring material to be selected can also be able to cope with the temperatures it is likely to encounter without brittleness while in function. For instance, parts made of silicone rubber would be ideal for usage in areas with varying temperatures since it can expand and shrink on condition of temperature variation and still offer elasticity.
The choice of the right material for the working temperatures enables one to achieve the O-ring’s sealing capacity and its ability to withstand the Service Conditions for an extended period. Thus, the choice of O-ring material for any particular application must take into account its service temperatures, since the operation of the O-ring at temperatures different from its ideal value can cause its destruction and, therefore, leakage and possible damage to the system.
Chemical Compatibility
Chemical compatibility is another relevant consideration when it comes to choosing rubber O-rings. The material of the O-ring must be also chemical safe, meaning that after a required period of time, it would not undergo changes that can make it to be out of bound for its function of sealing. For instance, acrylonitrile rubber (Nitrile rubber) is the best type of rubber for those applications which require it to come contact with oils and fuels while ethylene propylene diene rubber (EPDM Rubber) is best suited for those applications where it comes in contact with water or steam.
Selecting an O-ring material that is chemically compatible resists degradation and degradation when exposed to the chemicals that it will face, ensuring that it will last through its intended use without failing. Accordingly, an improper selection of material may result in chemical attack, swelling or even subsequent cracking of the gasket thus negatively affecting the seal or even damaging the system altogether.
Pressure Resistance
Some critical factors that determine the suitability of an O-ring include resistance to the pressures that it is likely to come across. The O-ring must be made of material that is suitable for the operating pressures of the item in which it is being used and be designed in such a way that the pressure will not extrude or deform the O-ring and weaken the seal. When marginal run pressures are required, materials such as Viton rubber or nitrile rubber are used in high-pressure applications due to their advantageous mechanical characteristics.
Choosing an O-ring that can withstand the operating pressures ensures that the O-ring will remain fully functional and for this reason determine the O-ring’s ability to seal properly to avoid leaks. When an O-ring is selected or used which in no way can meet the pressure rating required for the system, then it can fail and this may cause some of the following consequences: The whole system may fail and this may expose the users to many dangers.
Size and Shape
The cross sectional profile and its size of the O-ring must always correspond with the groove or the housing in which the ring is to be fitted. O-rings can be ordered and fitted precisely to suit serves or designed to work within a highly specific tolerance. Fitting this diviner as closely as possible to the object’s surface is also crucial to prevent leakage by using this pipe wrap.
Proper selection of the O-ring size and shape is important so that the O-ring forms a strong seal when used in an application. This is because if one chooses an O-ring with an improper size or shape it will not be able to function to the optimal standard, and this may lead to increased leakages and subsequent system failures.
Customization Options for Rubber O-Rings
Material Selection
Rubber O-rings are manufactured by selecting the appropriate raw material based on the requirements of the application in which the seals will be used. Various forms of materials have characteristics in terms of chemical stability; temperature tolerance; and mechanical properties. During the material selection, manufacturers can give assurance that an O-ring shall operate in the environment that O-ring is required.
Selection of material is another area that must be done in an appropriate technique so that the Custom O-rings of the right capacity can be developed to meet the practice needs. First of all, that is the choice of material: High temperature silicone rubber, nitrile for oil resistance, and the like – the selection of an appropriate material can be considered as the first stage of designing the right sealing system with reference to the application identified above.
Size and Thickness
It is possible to order these rings in standard or non-standard sizes, wall thickness and many other parameters. Thisorgtising makes it possible to have O-rings that will fit the other parts and also perform to the best of their ability out of the factory. However, the presence of custom O-rings, with their dimensions being adjusted to fit the needs of the system in question, can help improve the performance of the tasks in question.
The fact that the size and thickness of O-rings can be adjusted gives more versatility and confidence in the overall design that stays assured that the O-rings are adequate to the given requirements. All these aspects contribute to the development of a robust sealing solution since the manufacturers are keen to achieve a targeted level of accuracy.
Color
The use of color is not only for ornamental reasons since it can be useful in identification purposes as well as to distinguish between one O-ring and the other. Different colors have benefits in cases, where one might mistake an O-ring for another; by having the right O-ring in the right color, it means that errors can be avoided and time can also be saved.
These are additional benefits of custom color for O-rings, which may be important when integrating O-rings into a large and intricate system. At the end of the day, color customization is not a negative for custom rubber O-rings in terms of identification or aesthetic but rather an added bonus to the range of uses that these O-rings offer.
Special Coatings
It is also possible to modify the surface or the outer layer of these O rings to suit specific functions as required by the clients. For instance, coating can also serve as a lubricant where it can reduce the friction, offer chemical resistance and also other conditions. These grades of the coatings can help in the prolongation of useful life and sealing efficiency of the O-rings in rough operations.
Cautious heating and subsequent application of appropriate coatings on the specific O-rings can help to provide the seals with enhanced characteristics in various use areas to the optimum level. By having to do with service conditions such as wear and tear, and chemical immersion laws, protections provide a level of optimized functionality which boosts the general efficiency of customized rubber o rings.
Manufacturing Process of Custom Rubber O-Rings
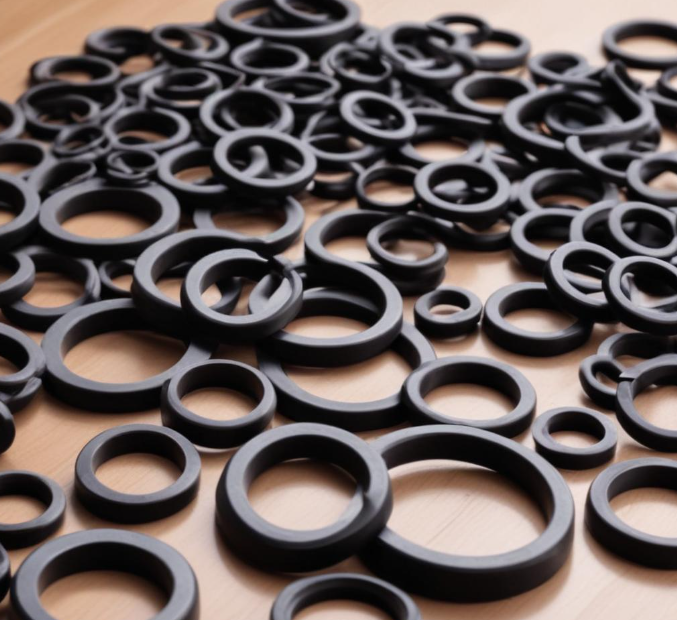
Material Compounding
Custom rubber O-rings are manufactured by going through several stages, of which material compounding entails blending of the raw rubber with other ingredients to obtain the required characteristics. This is a very important step because it enables one to achieve the end result of the product they are designing while meeting the needs of the particular application. The choice of additives for the compounding process includes finding materials capable of improving characteristics such as flexibility, resistance to chemicals, and stability in high temperatures.
This means that the materials being compounded are used as the basis of the manufacturing process especially with respect to the O-rings performance. Thus, different types of rubbers are produced by choosing and incorporating the right combinations of the most suitable ingredients for the best properties required in an application.
Molding Techniques
The preferred methods of molding custom rubber O-rings include injection molding, compression molding and transfer molding. That each method is beneficial in some way, and is used depending on the characteristics of the O-ring. Injection molding is well suited for small parts, with high-production rates while compression molding is well suited for large and more complicated shapes.
Regarding the molding process, it has been found that the process of choosing the right molding technique is critical when it comes to the application of the custom O-rings to be used. By choosing the right method, the producers can guarantee that the O-rings will be manufactured with the right dimensions and characteristics to meet the specific requirements of an application, thus creating a long-lasting and efficient seal.
Post-Processing
As for the initial molding of the custom rubber O-rings, they are then followed by other processes which include trimming, inspection, and testing before being ready for deployment. Skiptoning is the process that removes any excess material coming from the molding process while inspection and testing are the processes that have the role to check whether or not the O-rings are conformed to the specifications or to meet the required performance.
Quality control is an imperative stage in the fabrication cycle and it allows the final product to be usable. Through systematic examination of O-rings for quality and performance and ensuring the O-rings meet the set quality as well as performance benchmarks, manufacturers are able to ensure that they are fit for the purpose for which they are intended for and offer a seal that is satisfactory and semipermanent to the intended purpose.
Quality Control in O-Ring Production
Inspection Methods
Quality control in production of O-rings entails checks on the product to ensure that it is fit for use by clients through the use of various tests. Some of the methods used for validation of the O-rings’ quality include visual assessment, measurements, and noninvasive tests. These enable personnel to find any flaws or variations in the quality that may impact the functionality of the O-rings.
This way of inspection is proper to make sure that the custom rubber O-rings produced are of good quality standard and have no flaw. In assessing the versatility, quality and performance of the O-rings, manufacturers are able to offer more reliable sealing solutions that suit their customer requirements.
Testing for Performance
Thus, upon its manufacture, the O-ring must go through performance tests on the temperature range, pressure, and chemical compatibility. These tests are designed to impart the service conditions to which the O-rings will be exposed in their respective applications, thus ensuring they can maintain their sealing characteristics under operation of different conditions. Static testing is used to confirm that the custom O-rings are strong and can be used repeatedly without having to be replaced.
When selecting rubber material for a custom O-ring, applying physical tests checks if the O-rings meet the full requirements of the specific application intended for them. This is made possible by exposing the O-rings for testing purposes so as to ensure that when fitted into their applications they will hold a seal, and at the same time perform optimally in different conditions.
Certifications and Standards
Proper standards and certification of the manufactured products and materials ought to be met in specific industries and uses for example the medical use and in the aerospace industry. Such standard has to be met by custom rubber O-rings to ascertain that they are really safe for their intended usage. Affiliations by recognized bodies like the ISO and FDA approval help to confirm that the O-rings meet the right quality and performance standards.
Adhering to industry practices and standards while pursuing certification can be advantageous in guaranteeing the safety of custom rubber O-rings. These certifications give confidence to the customers that the O requires their professional level, above all in terms of technology.
-The rings are of high quality and hence fit to serve the specific purpose they are meant for in their respective settings.
Conclusion
The O-rings created from rubber are widely used in a variety of sectors as seals since they offer excellent protection and improve the operation of many systems. Due to the combination of the flexibility of the material, the size and the properties of the O-rings mentioned above these O-rings can fit various requirements of the application areas as automobile, aerospace, medical or even food industries. recognizing the meaning of the right selection of the material and the requirements of the additional overlays guarantees that custom rubber O-rings meet the requirements of efficiency and longevity.
FAQs
Standard rubber O-rings are predetermined based on the need and standard market, however, custom O-rings are manufactured based on the customer’s need hence giving a better performance and reliability in various applications. It can be chosen with reference to its variety in terms of material, dimension and functional characteristics to provide a snug fit and tight seal.
Several factors must be considered in choosing the right material; these include the range of temperature the nut and bolt will be subjected to, the chemical environment, and the pressure conditions. It is important to decide on which expert or supplier to talk to in order to determine the best material for the job.
Of course, special ordering of rubber O-rings could be produced out of such materials that have gone through FDA requirements for food and sanitary contact correlation, free from contamination and intended suitable for mass production.
Looking at the made parameterized rubber O-rings, it is clear that they find application in car, airplane, medical, and food and beverage industries and in oil and gas industry and in electronics, where specific type of sealing is needed.