Introduction to Rubber Extrusion
Rubber extrusion is an amazing process whose economic function exceeds the limits of the rubber industry by applying it to the shaping of raw rubber materials into usable forms. Think about a rubber company located near you which creates rubber compounds from raw rubber and shapes of profiles which have specific cross-sections. This process is not only molding, it is also creating parts that enable the innovation of the automotive, construction, medical, and other industries. Considering that there are a lot of rubber manufacturing companies and suppliers, the local guide program will be helpful here, since it will guide businesses and individuals on how they access quality rubber products. Knowing about rubber extrusion is the very first and essential condition to making the most of this promising manufacturing process.
Rubber Extrusion Process
Rubber extrusion, when processed in the right manner, produces a texture that is meticulously perfect and is a perfect blend of precision and expertise. It actually initiates with the search of top quality raw materials such as EPDM, silicone, neoprene and nitrile each one with its unique build and uses. The initial procedure involves a collection of raw materials which are sent to a number of motley mixing and preparation schedules with a view to attaining characteristics of a desired rubber compound suitable for extrusion. Next, the formed granules are fed into extruders, which are machines specifically designed in order to process rubber into constant profiles of high accuracy and uniform elongation. But then, the fairy is within the limitations.
Ensure introductions of rubber compounds, molding procedures, and extrusion equipment in the understanding list is for making correct profiles that are up to the traditional industry standards. Such cares of this company about the details and expertise that stand it out on the market stage where this company has its products recognized by their fine performance, reliability, and durability.
Benefits and Applications of Rubber Extrusion
This is because the advantages of rubber extrusion in the manufacturing industry are not only associated with molding raw materials but also with waste management, custom design, and efficient production. This new way of production is full of different opportunities in different industries in the cases automotive, construction, medical and many others. One of the leading advantages is cost efficiency, as rubber extrusion makes the forming of complicated profiles a high-tech and standardized process buying minimal material in the process as waste.
Find out more about our EPDM Sponge Seals for superior insulation and sealing
Moreover, because of rubber extrusion manufacturing design, it is possible to develop unique and tailored components fitted to each application. This product quality is improved overall and can be adjusted to help overcome different kinds of challenges. Due to that, the rubber extrusion accomplishes fast production cycles, so there is a time hurried delivery of the quality product to satiate the market-phantasm. EPDM Rubber profiles extrusion is employed in many industries including automotive – automotive seals and gaskets, medical instruments – medical tubing and construction profiles applications prove the wide and deep impact of this technology on modern production.
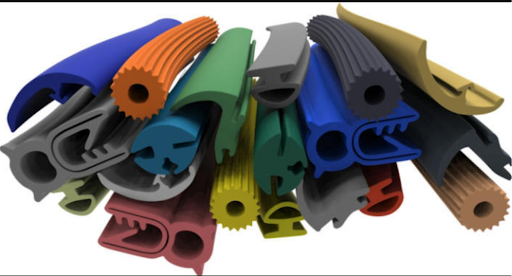
There are many Extrusion Processes of Rubber that exist:
The rubber extrusion domain combines processes to fulfill multiple requirements, both from the application and material perspectives. A typical example is hot extrusion, whereby the rubber material is heated past its melting point in order to enhance its malleability and aid the shaping processes become popular. Therefore, the melting process best applies to the materials that matter the environment so high temperature above the ordinary mark is required for molding and the material is not prone to heat-produced changes in properties. However, room temperature is crucial for the second process that is cold extrusion performed at room temperature and is preferred for rubber compounds sensitive to heat. The process of extrusion helps it to retain the overall structure and properties intact during the process, which is an important factor in application enablers.
The continuous vulcanization is markedly another discernible rubber extrusion operation being prepared and processed at the same phase. This joint approach raises the production efficiency without extracting curing agents after extruding them out. The process of vulcanization constantly (maximally) works for big production series in which the note of performance and constancy is undeniable. Via a close melding of these two processes, the manufacturers can eliminate many steps towards manufacturing the rubber products leading to reduction of the total processing time and making the rubber products of consistent quality.
Discover our Omega Shape Profiles for versatile rubber solutions
Key Components of Rubber Extrusion Machinery
Rubber Extrusion machines’ armature deals with the series of vital components that like the cogwheels constitute a machine, and transform the rubber materials into exact profiles. The main component of this modern machinery is the extruder, the device which enables the processing of rubber compounds. The extruder has 3 functions, namely feeding the fresh material, kneading it well, and applying pressure to push it through the die, by which the material is compressed. The die has a very strong influence on how the part of rubber turns to the profile that it wants, on what its cross-sectional shape, when it has what dimensions, and how it is finished on the surface.
Besides, the cooling cooling system of the extrusion machine that affects the temperature of the rubber extrudes to allow for the proper solidification and dimensional stability as well These cooling methods are often very important in avoiding the externalization or distortion of the produced articles. Following up, the cutting machine is used to cut the rubber of extruded form to lengths of identical sizes making sure the precision and uniformity in final products. And this is so that deterioration of the above components of the mini rubber profile extrusion system form a unbreakable system thereby the rubber extrusion can be reproduced in an effective and accurate manner, and so that rubber profiles of high quality for various industries can be produced.
Benefits and Applications of Rubber Extrusion
Rubber extrusion is a versatile manufacturing process that offers numerous benefits across various industries, making it a preferred choice for producing a wide range of rubber products.
Automotive Industry Applications:
In the automotive sector, rubber extrusion finds extensive applications in manufacturing critical components such as seals, weatherstrips, hoses, and gaskets. These rubber parts play a vital role in ensuring the optimal performance, durability, and safety of vehicles. Seals and weatherstrips prevent water and debris from entering vehicle interiors, contributing to passenger comfort and interior protection. Hoses and gaskets, on the other hand, facilitate fluid transfer and sealing of engine components, enhancing the overall efficiency and reliability of automotive systems.
Explore our range of Rubber D Seal Profiles
Construction Industry Applications:
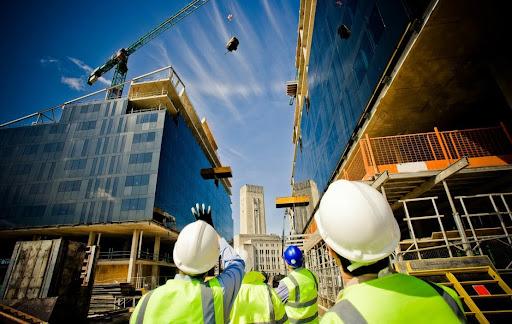
Rubber extrusion is also widely utilized in the construction industry to create essential building components like window seals, door seals, and architectural profiles. These rubber products offer effective sealing, insulation, and weatherproofing solutions for buildings, ensuring energy efficiency and environmental comfort. Window and door seals prevent air and water infiltration, contributing to improved energy conservation and indoor climate control. Architectural profiles, including rubber gaskets and trims, enhance the aesthetics and functionality of building facades while providing structural integrity and weather resistance.
Medical Industry Applications:
In the medical field, rubber extrusion plays a critical role in the production of specialized components such as medical tubing, catheters, and silicone implants. These precision-engineered rubber products meet stringent quality standards and regulatory requirements, ensuring patient safety, hygiene, and comfort. Medical tubing and catheters made through extrusion processes exhibit excellent flexibility, biocompatibility, and chemical resistance, making them suitable for various medical procedures and applications. Silicone implants, including breast implants and medical prosthetics, benefit from the durability, elasticity, and hypoallergenic properties offered by rubber extrusion techniques, enhancing patient outcomes and satisfaction.
Overall, the diverse applications and benefits of rubber extrusion underscore its importance as a cost-effective and efficient manufacturing method for producing high-quality rubber components across industries.
Challenges and Solutions in Rubber Extrusion
The technology of rubber extrusion has undoubtedly brought several benefits but by no doubt, there are some challenges manufacturers are expected to solve if the results are to be optimal. As with many other industrial processes, die swell is one of the most difficult problems to overcome, whereupon the extrusion of rubber keeps the diameter unpredictably expanding after leaving the die causing dimensional inaccuracies. Die designing optimized with features such as swell zones and precise provision of cooling can be helpful to deal with this issue and specifically get the product measurements.
The extrusion could be inconsistent in material properties and quality as curing at different rates is called for that across the extrusion profile. To expatriate this challenge, material formulation alterations, e.g., smartening the curing agents and additives are vital. Furthermore, the system with real-time monitoring and live feedback processes that can ensure the eradication of non-uniformity and the expansion of product quality overall must be put up.
One of the challenges in rubber extrusion is created by tons of waste materials which negatively affects both the economy and the environment. One of the ways of cutting down the waste generation is for manufacturers to employ eco-friendly practices, for example, by using the leftover materials, implementing efficient material handling systems and optimizing the machine trimmings for minimizing the extra materials trimming. These steps (not only) bring optimization in production expenditure but also aid in sustainability of the environment by decreasing the need for resources and garbage disposal.
Future Trends in Rubber Extrusion Technology
Rubber extrusion technology accompanies the future through furious improvements which aim at improving performance, sustainability, and cost-effectiveness. Nanoparticles and nanofillers as form of additives are being included in rubber blend to improve its mechanical properties, wear resistance, and thermal stability. Though infused by nanoparticles, these nano-enhanced rubber formulations provide improved characteristics and outperform the existing compounds used in several industries.
Recyclable materials are the essence of the rubber extrusion and these are gaining importance because of the fears of the environment which in turn are stimulating legislative rules. Producers are researching to invent rubber compounds from eco-friendly and recyclable natural resources to decrease the level of exposure to fossil fuels and resultantly, natural pollution. Integrated smart extrusion equipment, together with IoT sensors, automation, and data processing technologies is a vehicle of the revolution in the extrusion process. The systems are based on the intelligence which can improve the factors and even detect problems in the real-time and also ensure parasite maintenance therefore they result in better operation, reliability and cost cutting.
Sustainable operations are injuring the future of rubber extrusion where green technology, waste reduction, and circular economy headquarters are emphasized now. Recycling energy saving technologies like infrared heating, induction curing are being used for heating and cooling purposes to reduce energy consumption and greenhouse gas emission. The production waste can be not only recycled as part of the production processes, but also scrap materials can be reused and there can be a closed-loop system installed as a strategy to reduce waste and thus to limit environmental impact. Generally, they mirror a replacement of traditional, less sustainable, and rudimentary practices by new high-tech and efficient ones, therefore, enabling industrial players to advance and compete.
Conclusion
Along with this, rubber extrusion is of the critical manufacturing process that ensures cost-effectiveness, efficiency, and variation for many purposes. Being that deficits like irregular flow, and wasting on the whole material may occur, the innovative solutions and technological progress are developing the extrusion efficiency and product quality regularly. Trends, such as nano-additives, recyclable materials, smart machinery, and sustainability strategies, will be common in the future and scientists will work toward better rubber performance, reduced environmental impact, and improved industry functionality. Whether it is by remaining aware of these trends or by viewing technological advancements on rubber extrusion as a positive implement to follow, businesses would attain top quality, sustainability objectives, as well as the competitive advantage.
Contact us today to discuss your rubber extrusion needs and explore our full range of products
FAQs
- What is rubber extrusion, and how does it differ from other rubber manufacturing processes?
- What are the key benefits of using rubber extrusion in various industries like automotive, construction, and medical?
- Can you explain the different types of rubber extrusion processes and their applications?
- What are the challenges commonly faced in rubber extrusion, and how can they be addressed?
- How does the selection of raw materials impact the quality and properties of extruded rubber products?
- What are the key components of rubber extrusion machinery, and how do they contribute to the manufacturing process?
- What are some future trends and advancements expected in rubber extrusion technology, such as sustainability initiatives or innovative materials?