Introduction
This is a comprehensive discussion of the molded rubber products world in which we talk about applications, production methods, their benefits and available innovations for enhanced performance. Various moldings of rubber can be used as parts in different industries such as rubber diaphragm, and rubber grommets that form a comprehensive group that contribute to the production process. These products are characterized by strong resistance, unique customization, and dependable sealing solutions, making them valuable in different applications.
Key Features and Benefits
Durability and Flexibility
Rubber products that are molded are a fantastic choice for their exceptional condition of serviceability and adaptability that they readily offer in heavily industrial surroundings. They can operate in extreme conditions thanks to their resistance to various temperature and chemical exposures, even significant mechanical loads. Such durability guarantees a longer period of use and excludes any need for a frequent tote change, stimulating both cost-cutting and an operation of high efficiency.
Customization Options
Another benefit of molded rubber is its high capability to be made in desired dimensions corresponding to given parameters. The material composition, hardness, shape, and size of molded rubber products can be customized by manufacturers to meet very specific requirements across a number of industries. This tailorizing makes it possible custom-fitted for many different applications, maximizing the performance and functionality.
Types of Molded Rubber Products
Rubber Seals
A seal made up of rubber is one of the important accessories commonly used to prevent leakage and to help achieve a tight seal with different manufacturing equipment and pipelines. They are good to strain hardness, temperature and chemical in various industrial uses. Rubber seals, also the pieces of the hydraulic systems, engines, and manufacturing concerning retaining fluid, guarding against contamination contribute to the efficiency and reliability of the hydraulic systems, engines, and fabrication processes.
Rubber Gaskets
Gaskets fabricated from molded rubber have grasped the attention of the market as they have been proclaimed as the ideal sealing techniques in engines, pumps, and pipelines. They are capable of withstanding overcoming all above factors, such as overload, temperature variations and chemicals penetration, and takes care of all leakages in the system. Rubber gasketing is used across automotive, aircraft, and industrial applications, providing sealing that ensures for safe operation at maximum performance.
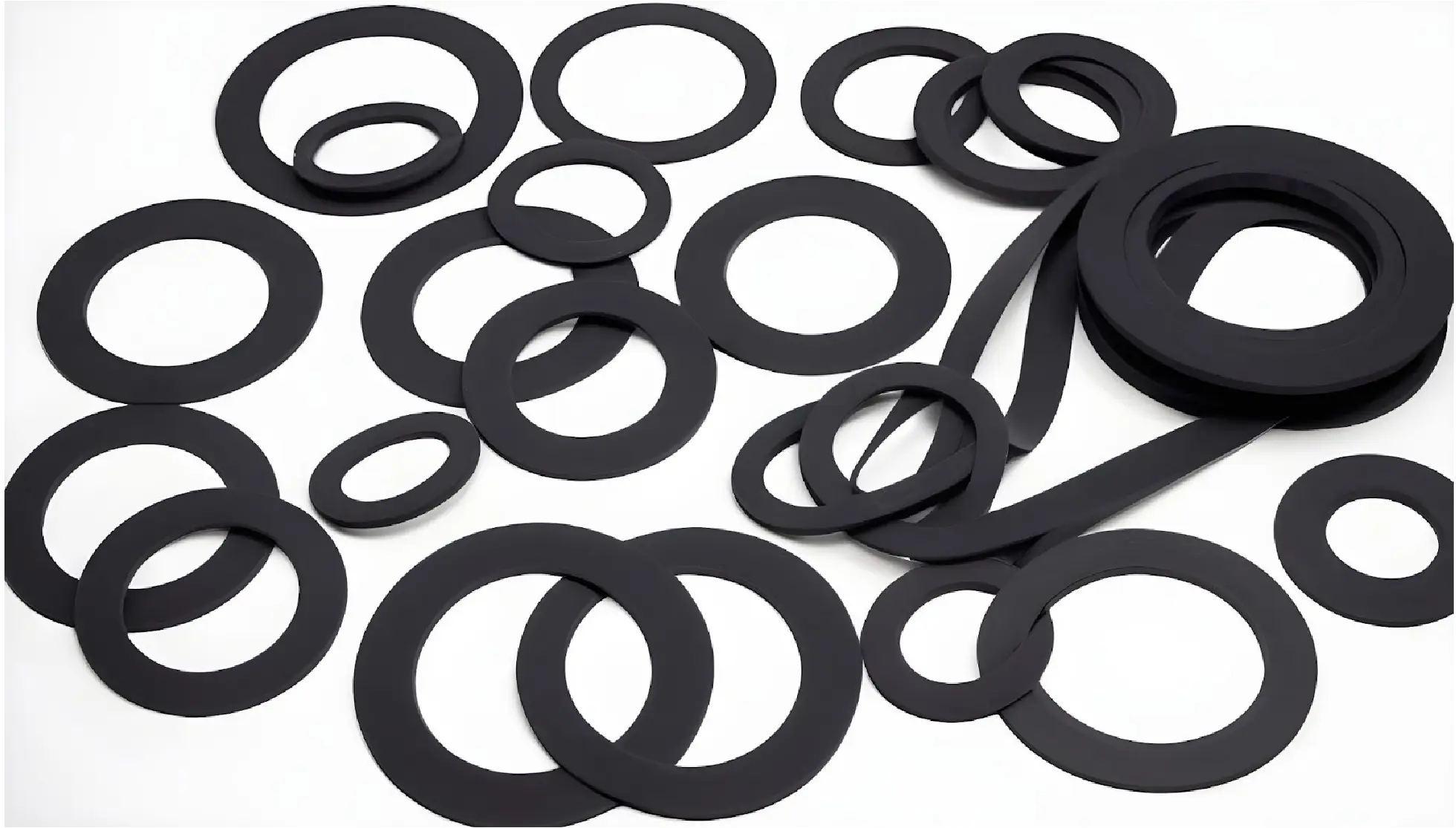
Rubber O-Rings
O-rings are multifunctional sealing units used in the hydraulic systems, plumbing, and industry facility operations. They function as an assuring seal and keep a zero-leaks probability, with mating surfaces linked under secure connections. O-ring configurations that are molded from materials such as EPDM, silicone, and neoprene have very fine limits of deformation, are resistant to chemicals, and will maintain stable mechanical properties over a wide temperature range, tolerance, making them suitable for almost all uses.
Rubber Diaphragms
Rubber diaphragms are thin, rubbery membranes that are typically used in pumps, valves, and regulators to control the amounts of flow, pressure and volume of fluid. They deliver qualified and scheduled working processes, enabling the continuous regulation of the operation and systems. Rubber diaphragms are key components of car and machinery production, medical equipment and the industry where reliability and fluid management are given as high priority.
Enhance Your Operations with Rubber Diaphragms!
Contact Us to learn more and find the perfect diaphragm solutions for your applications.
Rubber Over Molding
Rubber over molding means inserting a particular part into a rubber and tightening it to ensure better grip and dampening effect and to insulate against certain conditions. As a result, thi brings the field to the humanization of the tools design, the devices and the electronic machines, so that they would be comfortable to use and safe for both workers and people. A 3D molded rubber is a standard component of consumer goods, medical devices, and industrial tools that have been utilized in them to improve functionality and user satisfaction.
Rubber Bushes
Rubber bushes, or rubber bushings, are vibration-absorbing parts utilized in automotive suspensions, machinery mounts, and electrical apparatuses. They generate low profiles and low drilling sound, effectively resulting in less noise, wear, and stress. The bushes made from rubber provide anti-vibration padding which ultimately translates into less wear and tear with applications, and hence, the smooth operation, stability, and longevity of the vehicles, machinery, and appliances.
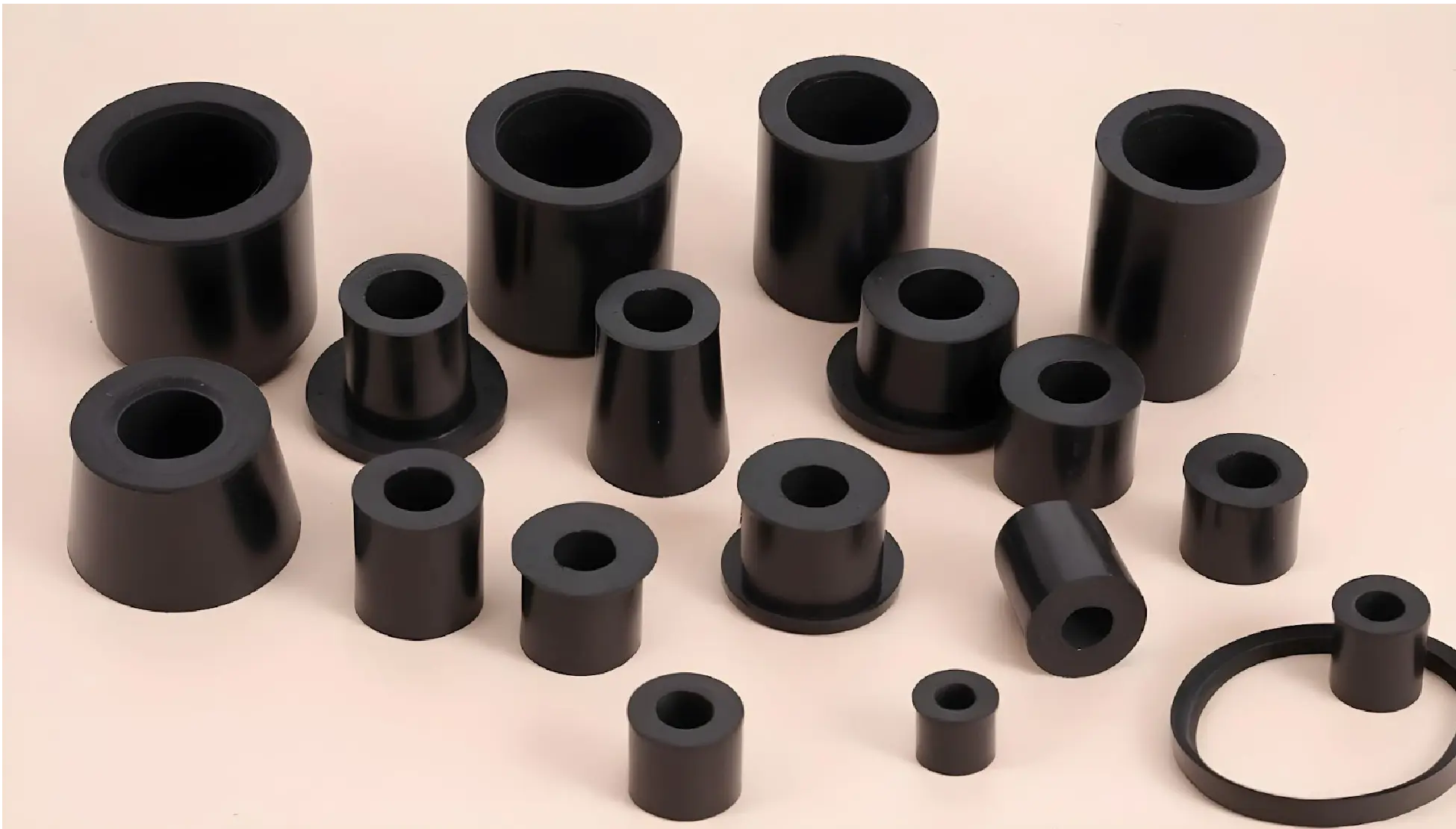
Rubber Vacuum Cups
Vacuum cups are the sucking devices widely applied in robotic, packaging, and logistics automation machinery. Accuracy and stability of positioning is essential to any automated process which happens for the reason of autonomous grasping and lifting. Rubber vacuum cups are the important components of industries ranging from manufacturing to logistics as well as robotics where getting consummate doings with objects is critical.
Rubber Rollers
Rubber rollers refer to round artifacts found in printers, machinery, and material processors. These machines are meant to operate at the various stages in the process; for example, they may handle, compact, or mold materials as they facilitate quality production. Rubber rollers offer the strength, flexibility and precision needed for various industrial functions hence being among the most industrious equipment in production facilitation.
Rubber Bellows
The rubber bellows, or expansion joints, are flexible connectors, which are used in the piping systems to transmit movement, vibration and thermal. expansion. They accommodate changes when dimensions of the system are altered keeping the sealing intact, which prevents leaks and other possible harms. The rubber bellows help to keep HVAC systems operating under challenging conditions and the usefulness of the bellows so much that the same applies for automotive exhausts and industrial piping networks.
Rubber Grommets
The rubber grommets are protective rings useful in wiring terminations, cable management and automotive vehicle applications. They protect, isolate, and position electrical and hydraulic lines and tubes safely which minimizes repair or replacement costs. Rubber grommets take on very important roles by preventing electrical hazards, proper organization to keep electronics together, and security against possible moves elsewhere. They are installed in household appliances, automotive wiring harnesses and other circuit boards.
Applications in Various Industries
Automotive Sector
Rubber parts manufactured by molding method play the central role in the automotive industry for the production of seals, gaskets, hoses, bushings, and also vibration dampeners. They not only improve the performance, reliability and lifespan of vehicles, but also really make the difference in sealing effects and vibration suppression.
Manufacturing Industry
In manufacturing, molded plastic feedstocks such as diaphragms, gaskets, rollers and bellows substantially contribute to the efficiency of a machinery, the quality of the product, and the operational safety. They have advanced accuracy, tightness that does not provide any leaks , and also have distributed motion that ensures a perfect and seamless operation.
Medical Field
The rubber mold generally plays a key role in the medical industry owing to medical devices, equipment, seals, and grommets that are produced for the same. On the other hand, their quality and administrative specifications are tough to fulfill. They guarantee patient security and medical applications’ reliability.
The Rubber Manufacturing Process
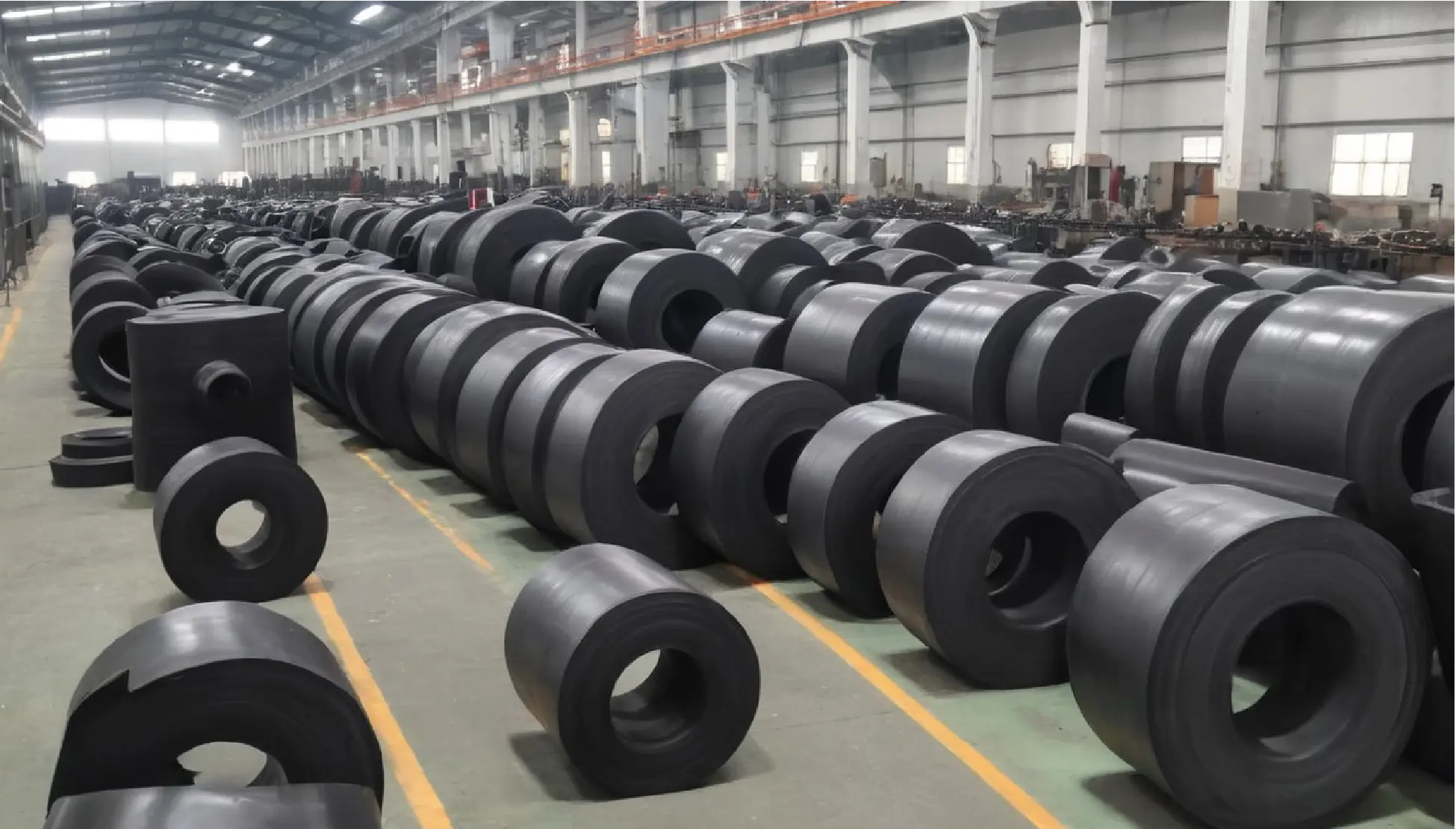
Raw Material Selection
Raw material selection initiation lies at the basis rubber manufacturing process, wherein high-grade compounds based on synthetic rubber are tailored to specific app and performance requirements. The manufacturers evaluate materials and their ability to stretch, harden, chemical resistance, and the tolerance to a particular temperature.
Mixing and Preparation
Input raw materials go through specific processing – compounding, milling and calendaring. This is a procedure that guarantees that the finished product has a particular shape, color, sizes, texture, specification and these are often known to be oil resistant, cut resistant, water resistant and they always employ the vulcanized form of chemicals in the process.
Extrusion and Molding
Shaping of the raw body through extrusion and molding processes makes up for all due profiles, forms, and dimensions needed. Techniques including injection molding, compression molding, and transfer molding are used by manufacturers to create molded rubber products that have high precision and accuracy. This is helpful because the products will be of the approved dimensions, as well as making replications easier.
Vulcanization and Curing
The vulcanization process encompasses the treating of the rubber products molded by means of heat and additives, which aims at increasing cross-linking and bonding within molecular structure. Rubberization not only renders rubber an excellently-wearing material, it also makes the actual rubber products increasingly stronger, more resilient, and more durable – a foundation for consistent operation in all conditions.
Quality Control and Testing
Quality control measures being incorporated throughout the rubber manufacturing process in order to be stricter ensure product safety and compliance. Molded rubber parts are produced only after inspecting raw materials, conducting dimensional checks, proving their performance, and making sure the products are in line with industry standards; thus they are highly reliable, functional, and safe.
Environmental Impact and Sustainability
Eco-Friendly Materials
Next generation elastomeric materials (bio rubber) is here (available), whose base ingredients are derived from natural rubber, recycling materials and bio-based compounds will increment sustainable practices among manufacturers. Companies may focus their efforts on lowering their contributions to pollution and implementing recycling practices as part of an ecosystem approach by choosing environmentally friendly materials and improving their waste disposal.
Recycling and Waste Management
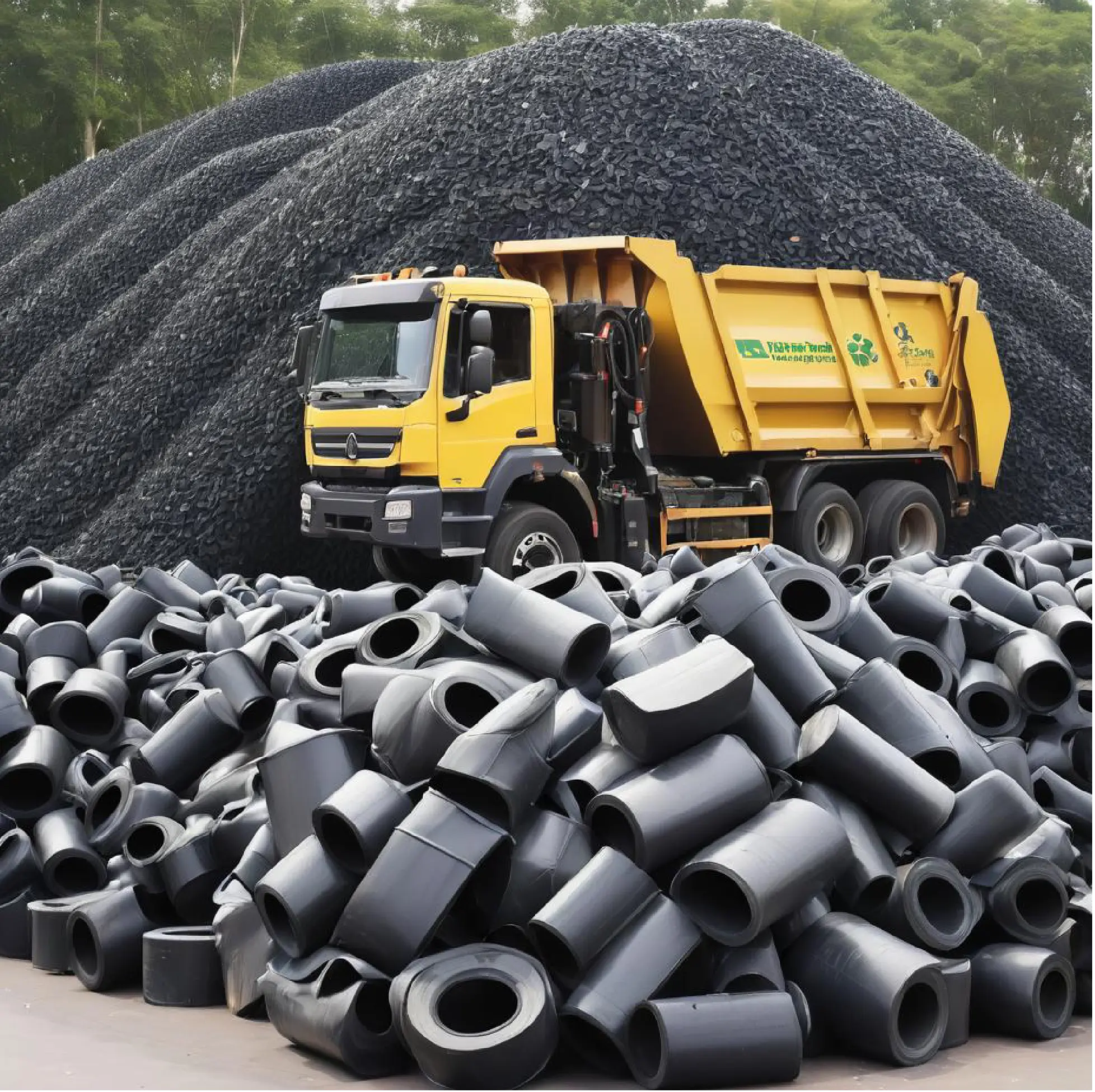
Sustainable practices are a key focus area of rubber manufacturers by accepting recycling approaches, upcycling waste materials, employing closed-loops, and streamlining logistic processes. Thus, such practices help to reduce the depletion of resources, waste generation, and the effect on the environment that in turn contributes to a sustainable consumption pattern and environmental obligation.
Future Trends in Molded Rubber Products
Advanced Materials and Technologies
Development of new rubber formulations, application of nanotechnology, use of smart rubber materials and additive manufacturing play a key role in implementing progress through performance, lifetime and range of application. Producers are actively coming up with alternative materials and methods of production to satisfy the economic requirements. Also they are accurate in their technological advancements.
Industry 4.0 Integration
The digital technology such as automation, predictive maintenance, and real-time monitoring (RTM) has via the integration process become a critical part of the rubber manufacturing sector. Industry 4.0 paradigm is underlying the transformation of production processes by improving oftentimes talent and quality control, transparency and responsiveness to the markets. Automated Systems Are Trekked through the Production Process, Save Time and Increase the Workflow Efficiency in General. Predictive maintenance algorithms get into the data to detect and identify potential equipment issues that have a capacity to bring about disruptions, so that the maintenance timelines are well-organized and prolong trauma and damage. Real-time monitoring systems help to get to actionable information about the production success. Thanks to it, it will be possible to respond both quickly and continuously to the unexpected events and will allow carrying out the improvement initiatives.
FAQs (Frequently Asked Questions)
Here are answers to some common questions about molded rubber products and their applications:
- What are the key benefits of using molded rubber products?
- How are rubber diaphragms used in industrial applications?
- What are some common applications of rubber over molding?
- How do rubber grommets contribute to cable management?
- What environmental initiatives are undertaken by the rubber industry?
- What are the emerging technologies in the rubber manufacturing sector?
Conclusion
Exploring the world of molded rubber products reveals a landscape of innovation, sustainability, and versatility. Molded rubber components, ranging from seals and gaskets to diaphragms and grommets, play essential roles across industries, offering durability, customization, and reliable performance. As industries evolve and embrace technological advancements, molded rubber continues to be a cornerstone of modern engineering, providing solutions that meet diverse needs while contributing to a greener, more sustainable world. Embracing advancements in materials, technologies, and practices ensures a future where molded rubber products remain indispensable in various applications, driving efficiency, reliability, and environmental responsibility.
Looking for custom rubber products or specialized solutions? Contact Us today! Our team is dedicated to providing tailored products and excellent service to meet your unique requirements. Let’s collaborate and create innovative solutions together.
1 Comment
Comments are closed.