Rubber products play an integral role across a multitude of industries, ranging from automotive to healthcare, showcasing the critical need for stringent testing methodologies to uphold quality and performance benchmarks. The significance of these testing methods forms the core focus of this article, as it delves into the intricate world of rubber testing. This exploration aims to shed light on the diverse techniques employed to assess the quality, durability, and overall performance of rubber materials.
Such meticulous testing protocols are paramount not only for ensuring regulatory compliance but also for guaranteeing the dependable functionality of rubber products within their designated applications. Furthermore, these testing methodologies are instrumental in meeting customer expectations concerning safety standards and optimal performance outcomes.
Table of Contents
Introduction: Overview of Rubber Testing Methods
The realm of rubber testing methods encompasses a broad spectrum of techniques meticulously crafted to scrutinize the intricate properties of rubber materials. These methods serve as the backbone of quality assurance protocols, essential for verifying that rubber products align with stringent regulatory standards.
Moreover, they play a pivotal role in evaluating the durability and reliability of rubber materials, ensuring they can withstand the rigors of real-world applications across diverse industries. By subjecting rubber products to rigorous testing, manufacturers can guarantee not only their compliance with regulatory requirements but also their ability to deliver consistent performance and safety, thereby fostering trust and satisfaction among end-users.
Importance of Quality and Performance Standards
The importance of quality and performance standards cannot be overstated, especially concerning regulatory compliance within industries reliant on rubber products. Regulatory bodies set forth stringent guidelines and standards that dictate the composition, properties, and performance characteristics expected of rubber materials. These standards serve as a crucial benchmark for manufacturers, guiding them in producing rubber products that not only meet legal requirements but also uphold the highest levels of quality and performance.
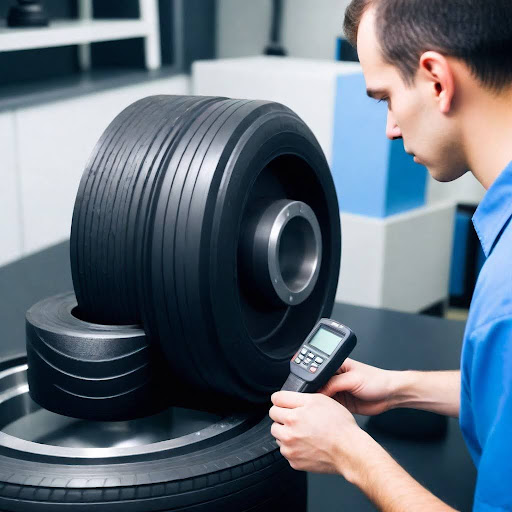
Explore Our Quality Rubber Products
Regulatory Compliance
Adhering to quality and performance standards is paramount for regulatory compliance in industries where rubber products are utilized. Compliance with these standards ensures that rubber products meet the criteria set by regulatory bodies, safeguarding against potential legal issues and ensuring the safety and reliability of these products in their intended applications.
Ensure Regulatory Compliance with Our Rubber Solutions
Product Reliability and Safety
Quality testing is instrumental in ensuring the reliability and safety of rubber products. Rigorous testing methods help identify potential defects, weaknesses, or inconsistencies in rubber materials, enabling manufacturers to rectify these issues and produce products that meet industry standards and customer expectations. This proactive approach not only enhances product reliability but also contributes to improved safety standards, instilling confidence in the performance and durability of rubber products.
Enhance Product Reliability with Our Tested Rubber Materials
Customer Satisfaction
High-quality rubber products that undergo comprehensive testing are more likely to meet or exceed customer expectations. Consistency in quality and performance leads to increased customer satisfaction, fosters trust in the brand, and promotes long-term relationships with clients. By prioritizing quality testing, manufacturers can enhance brand reputation, build customer loyalty, and ultimately drive sustained success in the market.
Elevate Customer Satisfaction with Our Premium Rubber Products
Common Rubber Testing Methods
Rubber testing encompasses a variety of methodologies designed to comprehensively evaluate the properties and performance of rubber materials. These testing methods are critical in ensuring that rubber products meet stringent quality standards and perform optimally in diverse applications across industries.
Physical Testing
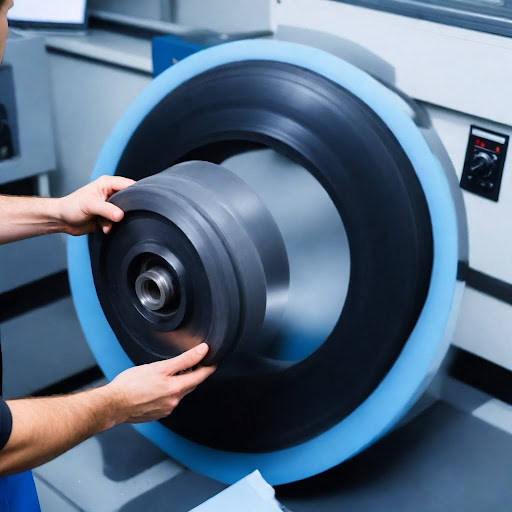
Physical testing is a fundamental aspect of rubber testing, focusing on evaluating a range of properties such as hardness, tensile strength, elongation, compression set, and resilience. These tests provide valuable insights into the physical characteristics of rubber materials, helping determine their suitability for specific applications.
For instance, hardness testing assesses the resistance of rubber to indentation or penetration, which is crucial in applications where abrasion resistance is paramount. Tensile strength testing measures the maximum stress a rubber specimen can withstand before breaking, providing vital information about its durability and load-bearing capacity.
Elongation testing determines the ability of rubber to stretch under tension, essential for applications requiring flexibility and resilience. Compression set testing evaluates the material’s ability to recover its original shape after being compressed, indicating its resistance to deformation over time. Resilience testing measures the energy absorption and recovery of rubber, indicating its ability to withstand impacts and shocks. Collectively, these physical tests play a crucial role in assessing the overall performance and suitability of rubber materials for various industrial applications.
Chemical Analysis
Chemical analysis is another essential aspect of rubber testing, focusing on evaluating the chemical composition of rubber materials, including the presence of additives, fillers, and contaminants. This type of testing is critical for ensuring that rubber products are free from harmful substances and meet stringent chemical compatibility requirements.
Chemical analysis techniques such as spectroscopy, chromatography, and mass spectrometry help identify and quantify specific chemical components in rubber materials. For instance, infrared spectroscopy can detect functional groups and chemical bonds in rubber compounds, providing insights into their molecular structure and composition. Gas chromatography-mass spectrometry (GC-MS) can identify and quantify trace amounts of additives or contaminants in rubber samples, ensuring compliance with regulatory standards.
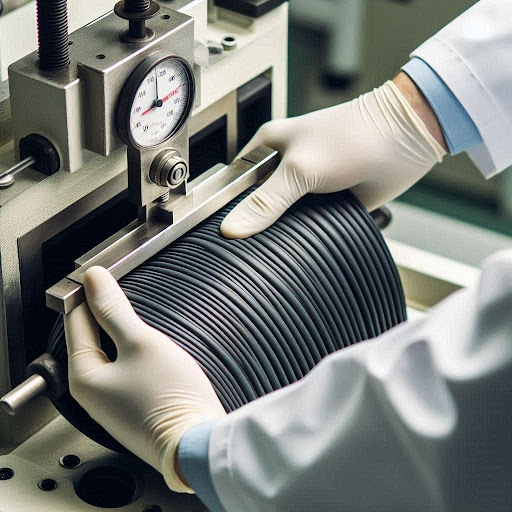
Chemical analysis also includes testing for specific chemical properties such as pH, acidity, alkalinity, and moisture content, which are crucial in determining the chemical stability and performance of rubber materials in various environments. Overall, chemical analysis plays a vital role in ensuring the safety, quality, and performance of rubber products in diverse applications.
Mechanical Testing
Mechanical testing focuses on evaluating the mechanical properties of rubber materials under different conditions, including stress, strain, fatigue, and wear. These tests provide valuable information about the structural integrity, durability, and performance capabilities of rubber products, helping manufacturers assess their suitability for specific applications.
For instance, tensile testing measures the force required to stretch a rubber specimen to its breaking point, providing insights into its tensile strength and elongation properties. Flexural testing evaluates the bending and flexing behavior of rubber materials, essential for applications where flexibility and resilience are critical.
Compression testing assesses the material’s ability to withstand compressive forces, indicating its load-bearing capacity and resistance to deformation. Shear testing measures the material’s resistance to shear or cutting forces, relevant in applications where shear strength is essential, such as in seals and gaskets.
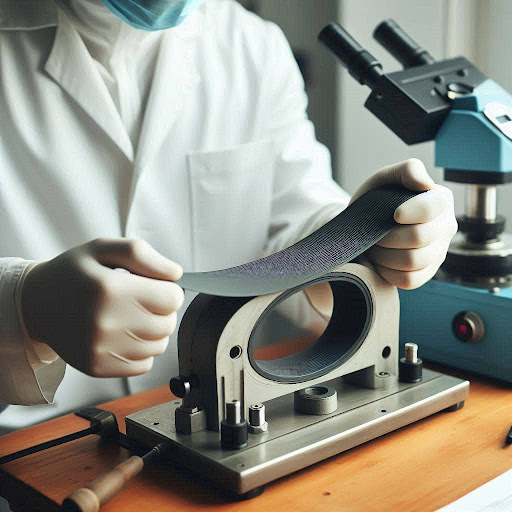
Fatigue testing evaluates the material’s resistance to repeated loading and unloading cycles, simulating real-world usage conditions and predicting its fatigue life. Wear testing assesses the material’s resistance to abrasion and wear, crucial for applications exposed to abrasive conditions or mechanical friction.
Impact testing evaluates the material’s ability to absorb and dissipate energy under impact loads, indicating its toughness and shock resistance. Overall, mechanical testing provides comprehensive insights into the mechanical behavior and performance of rubber materials, aiding in the design, development, and optimization of rubber products for specific industrial applications.
Environmental Testing
Environmental testing involves simulating real-world conditions, such as temperature extremes, UV exposure, moisture, and chemical exposure, to evaluate how rubber materials perform under environmental stressors. These tests help predict the long-term durability, reliability, and performance of rubber products in different operating environments.
For instance, temperature testing assesses the material’s behavior under extreme temperatures, ranging from sub-zero conditions to high heat, simulating winter and summer conditions. UV exposure testing evaluates the material’s resistance to ultraviolet radiation, which can cause degradation and discoloration over time.
Moisture resistance testing assesses the material’s ability to resist water penetration and moisture absorption, crucial for applications exposed to wet or humid conditions. Chemical exposure testing evaluates the material’s resistance to chemicals, acids, solvents, and oils, ensuring compatibility with specific substances and environments.
Environmental testing also includes accelerated aging tests, where rubber materials are subjected to accelerated aging conditions to simulate long-term exposure and predict their aging characteristics and performance degradation over time.
Overall, environmental testing provides valuable insights into the environmental resilience and long-term durability of rubber products, aiding in the selection of materials and the development of products that can withstand challenging environmental conditions.
By employing these comprehensive rubber testing methods, manufacturers can ensure the quality, durability, reliability, and safety of rubber products across various industries, meeting regulatory requirements, customer expectations, and industry standards.
Quality Control Processes in Rubber Testing
Sampling and Preparation
Quality control starts with proper sampling and preparation of rubber specimens. Samples must be representative of the product or material being tested, and preparation methods should minimize variability and ensure accurate test results.
Testing Equipment and Procedures
State-of-the-art testing equipment and standardized testing procedures are essential for reliable and repeatable results. Calibrated equipment, adherence to testing standards, and trained personnel contribute to the accuracy and validity of test data.
Data Analysis and Interpretation
Data analysis involves interpreting test results, comparing them against established standards or specifications, and drawing meaningful conclusions. Statistical analysis, trend monitoring, and data visualization techniques aid in understanding the performance characteristics of rubber materials.
Advancements in Rubber Testing Technology
Automation and Robotics
Automation and robotics are transforming rubber testing processes, enabling faster, more precise, and consistent testing procedures. Automated systems reduce human error, increase throughput, and enhance overall testing efficiency.
Non-Destructive Testing Techniques
Non-destructive testing techniques, such as ultrasound, infrared thermography, and X-ray inspection, allow for the evaluation of rubber materials without causing damage. These techniques are invaluable for assessing internal defects, structural integrity, and material properties.
Data Analytics and AI Integration
Data analytics and AI integration enable advanced data processing, pattern recognition, and predictive modeling in rubber testing. Machine learning algorithms can analyze large datasets, identify trends, predict material behavior, and optimize testing protocols for improved accuracy and efficiency.
Conclusion
Rubber testing methods play a pivotal role in ensuring the quality, reliability, and safety of rubber products across industries. By adhering to stringent quality and performance standards, manufacturers can deliver high-quality products that meet regulatory requirements and customer expectations. Advancements in testing technology, coupled with robust quality control processes, continue to drive innovation and excellence in the rubber industry.
Unique FAQs
- What are the primary regulatory considerations in rubber testing for different industries?
- How does rubber testing contribute to product reliability and safety?
- What role does quality control play in the rubber testing process?
- Can you explain the significance of environmental testing in evaluating rubber materials?
- How are advancements in automation and AI impacting the future of rubber testing methods?